Launching Lenzing and Mill partnership
- Alison Jose
- Jul 22, 2018
- 3 min read

STSC spend a considerable amount of time researching and connecting personally with the principle of a company before we decide to work with any supplier. There are several criteria for our working relationships and not least is the quality of the products, the care in the production, and the ease of communication we have together; a simpatico regarding how you care for people and the planet.
We are therefore especially thrilled to announce a partnership with one of India’s leading large commercial textile companies and ask them to produce STSC’s fabric using yarn made by Lenzing™ in Austria, the world’s most advanced company making sustainable biodegradable yarn for fashion.

What makes our new Indian partner so important is their dedication to doubling down on producing the very best sustainable textiles possible, and for their focus on water conservation.
STSC first became a recommended partner of Lenzing and chose to work with their only partner in India, who then gave me a glowing personal recommendation for this new supplier.

What’s key to know is that Lenzing™ produce yarn from wood pulp derived from sustainable renewable forests in Austria and Bavaria, having secured Europe’s highest standards for forestry accreditation. They then minimise their footprint by producing the yarn locally in their Austrian state-of-the art Closed Loop System factory which is accredited with almost zero waste and chlorine free production.
So, knowing this, it was of course equally important for me to find a textile company to produce my fabrics who uphold the highest ethical and environmental standards possible, and I am so very pleased to announce that I have 😊

With two locations in that state of Maharashtra, their core competence is in Yarn Dyed fabrics, Piece Dyed fabrics, and woven fabrics like organic cotton plus Lenzing™ branded viscose fibres Tencel™ and Lenzing’s very latest and most sustainable fabric, EcoVero™.
Even though this textile company is a large corporation they have adapted their business model to “not only save costs, but also focus on our contribution towards social responsibility for pollution reduction and to preserve a healthy environment for all living beings”.
The technology they have adopted proves that sustainable textiles can also be a true financially viable option for designers. They have created a production house with full capabilities, from design and development through to state-of-the art integrated manufacturing setups for yarn dyeing, weaving, fabric dyeing and processing.

It is however their impressive investment in water conservation and treatment that meant I wanted to work with them, over and above their competitors. In order to treat their waste water, they have invested in the latest Italian Biological Treatment Technology based Effluent Treatment System with capacity of 1200 kilo litres/day (KLD).
This System doesn’t require any toxic or hazardous chemicals for treatment as it works on a formula of treating effluent through organic bacteria and microorganisms. This accepted worldwide technology has brought a revolutionary change in the world of effluent treatment systems.

The System not only saves on the cost of effluent treatment, but also displays parametric results to fulfil the State’s Pollution Control Board statuary requirements.
Investment has continued with their Heat Recovery System which improves thermal efficiency and reduces coal consumption thereby reducing their carbon footprint.
Plus, all machines have been installed with Low Material To Liquor Ratio to reduce water consumption. Their installed Recovery systems such as the Caustic Recovery Plant helps reduce a generation of high TDS effluents to a great extent.
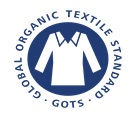
The company is accredited by both Oeko-Tex and GOTS (Global Organic Textile Standard) Certified with additional certifications in the process.

They know that care for the environment starts with strong design and product development from the fibre stage, and have therefore set up a comprehensive sampling facility, and continuously strive for futuristic products to create sustainable textiles.
This is illustrated in their investment in using Lenzing™ fibres, and especially being such an early adopter of Lenzing’s most advanced sustainable textile EcoVero™ which was only just launched in Austria in late 2017.
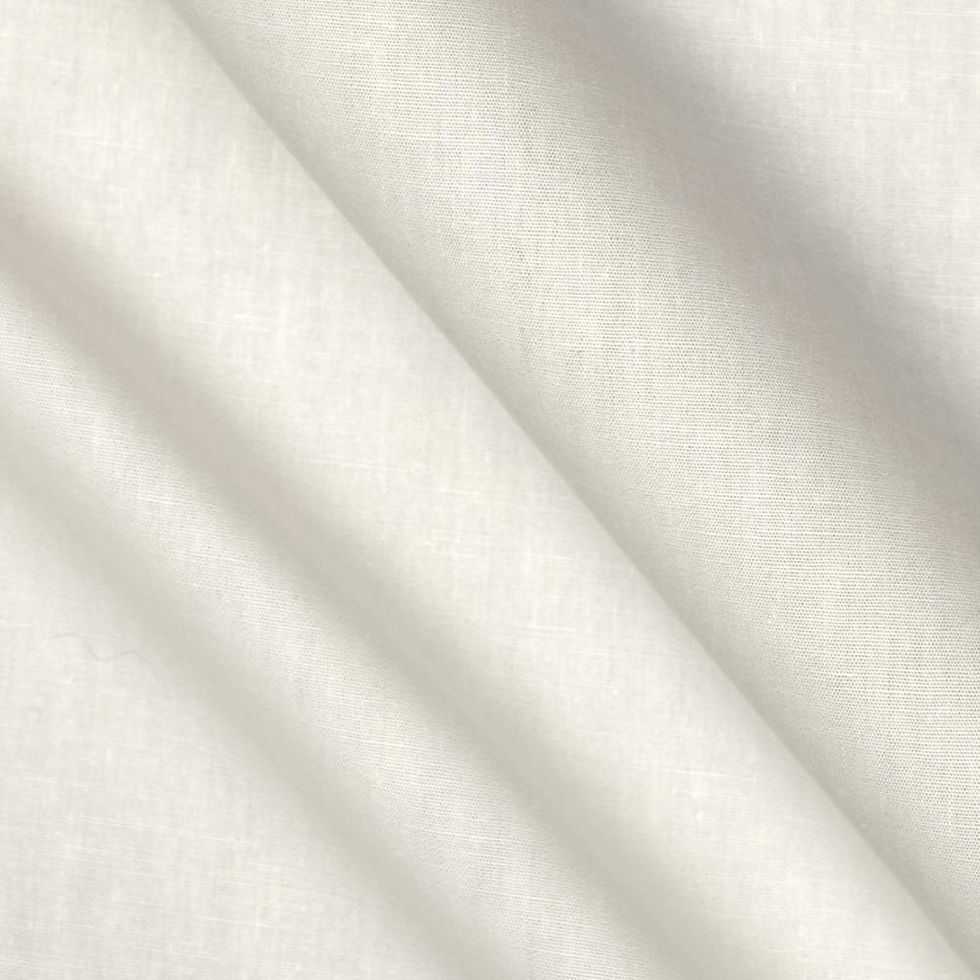
For further information on Lenzing™ and their textile production, plus how Tencel and EcoVero fibres are made, visit the links, SHOP online plus contact Alison Jose at STSC.
Comentarios